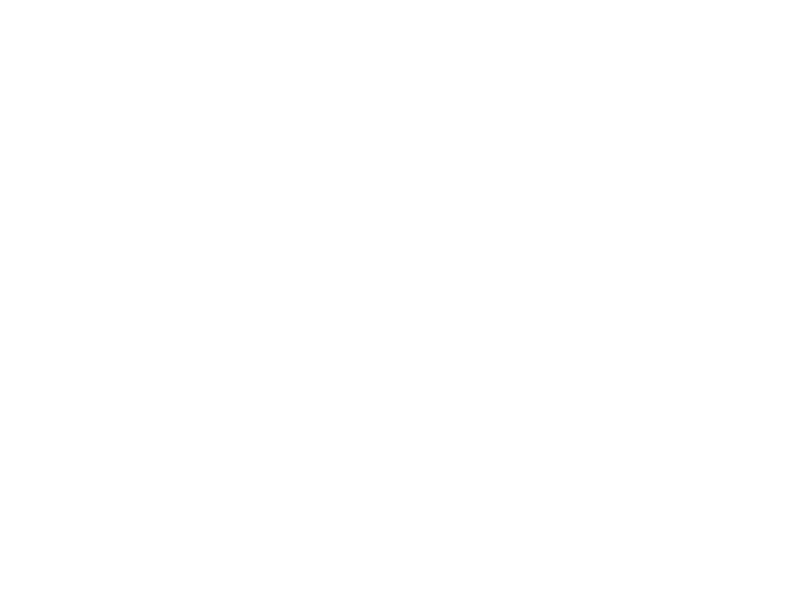
Applications of Silicon Nitride (Si₃N₄) Ceramic Balls in Wind Power Generation
Silicon nitride (Si₃N₄) ceramic balls are increasingly critical in wind power systems due to their high strength, wear resistance, lightweight properties, and corrosion resistance. Below are their key applications and technological advantages:
1. Main Shaft Bearings
- Application: Used in high-load bearings supporting the wind turbine main shaft.
- Advantages:
- Lightweight: 40% lower density than steel, reducing rotational inertia and improving startup efficiency.
- Fatigue Resistance: 3–5× longer lifespan under cyclic loads (e.g., wind speed fluctuations).
- Self-Lubrication: Minimizes grease dependency, ideal for offshore humidity.
2. Gearbox High-Speed Bearings
- Challenge: Gearboxes are prone to failure due to friction and micropitting in steel bearings.
- Si₃N₄ Solution:
- Low Friction (coefficient: 0.1–0.2), improving gearbox efficiency by 1–3%.
- Electrical Insulation: Prevents current corrosion from inverters (critical in doubly-fed turbines).
- Case Study: Siemens Gamesa’s 2024 offshore 8MW turbine trials saw a 60% drop in failures.
3. Direct-Drive Generator Bearings
- Trend: Gearless designs demand ultra-reliable bearings.
- Si₃N₄ Benefits:
- Electrical Isolation: Blocks shaft currents, protecting generator electromagnetics.
- Cryogenic Stability: Performs reliably in Arctic projects (–40°C) without brittleness.
4. Harsh Environment Adaptability
- Offshore Wind:
- Salt Spray Resistance: Zero rust over 20+ years.
- Biofouling Prevention: Smooth surface inhibits barnacle adhesion.
- Desert/Dusty Regions:
- Abrasion Resistance: Superior to steel in sand-laden environments.
5. Future Directions (2025+)
- Hybrid Bearings: Combine Si₃N₄ balls with steel races for cost-performance balance.
- Smart Monitoring: Embedded sensors for real-time stress tracking (e.g., SKF’s Smart Bearing).
- Additive Manufacturing: 3D-printed complex geometries for 15MW+ turbines.